Composites
Using custom resin systems of epoxy, polyester and vinyl esters, plus various glass and carbon fibers, Janco manufactures composites with the precise mechanical, electrical and temperature properties needed in many industrial applications.
- Excellent dieletric qualities
- Outstanding mechanical strength
- High strength-to-weight ratios
- Low thermal conductivity
- Dimensional stability
- Chemical resistance
- Corrosion resistance
- Pigmentability
Products
Our sales and engineering staff will consult with you to identify the composite materials that will best serve your needs and the properties essential to your application. Our custom processes can be utilized in multiple design options including filament winding and pultrusions. We use UL certified and performance grade materials. A variety of finishes and coating can further enhance your products.
Filament Wound Tubing
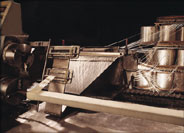
Filament winding is a process which draws reinforced filaments (continuous strands), mat or veil through a resin bath and winds them onto a mandrel. Winding can be helical or circumferential depending upon desired performance characteristics. Wind angles and resin volume/content can also be varied to meet your specifications. When the desired exterior diameter has been reached, the tube is removed and oven cured under controlled temperatures. When curing is complete, the mandrel is removed and the part is ready for fabrication.
Janco is one of the few companies that produces filament wound tubes with inserts or over core materials, offering the design engineer unique design options. Our sales/engineering staff will consult with you to select the mandrel shape and diameter, thermoset resins and type and orientation of reinforcement fibers that will produce the performance characteristics required by your application. Whether it's high-strength, electrical-resistance or a need to meet demanding temperature requirements, Janco can develop a custom solution for you.
Advantages of Filament Winding
- High strength
- Low density
- Readily machineable
- Excellent insulator
- Corrosion resistant
- Highly repetitive fiber placement (part-to-part, layer-to-layer)
- Strong, thin-walled, lightweight composites can be produced
- Can be made translucent
Applications for Filament Wound Tubes
- Antennas
- Battery casings
- Bridge plugs
- Bearings and collars
- Bushings
- Cylinder tubes
- Cryogenics
- Equipment and tool handles
- Filter housings
- Fuse tubes
- High voltage insulators
- Impeder tubes
- Pressure tubing
- Structural tubing
- Water and wastewater treatment components
Pultruded Shapes
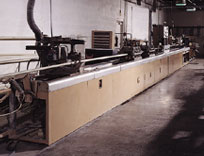
Like our filament wound products, Janco pultrusions are engineered to provide the combination of physical properties essential to your application. In the pultrusion process, reinforcement fibers (roving, mat, cloth or veil) are pulled through a polyester, epoxy or vinyl ester resin bath and then through a heated die where the polymerization of the thermoset resin matrix takes place. The profile of the pultrusion is determined by the shape of the die. The cross sectional profile is then automatically cut to specified lengths. Common shapes include:
- Rods
- Tubes
- Bars
- Profiles
- Angles
Advantages of Pultrusion
- High strength
- Lightweight
- Corrosion resistant
- Excellent electrical insulator
- Thermal insulation
- Non-magnetic
- Non-conductive
- Available in custom colors
- Dimensionally stable
Applications for Pultrusions
- Structural shapes
- Transformer spacer sticks
- Hot-line maintenance tools
- Standoff insulators
- Fuse tubes
- Water and wastewater treatment components
- Sporting goods